While physical threats such as machinery and chemicals are obvious, there are numerous hidden hazards in the industrial workplace that are often underestimated. However, these risks can be just as devastating as the more obvious hazards. What are those risks, how do we address them, or rather, how do we take a proactive approach to maintaining a safe and healthy work environment?
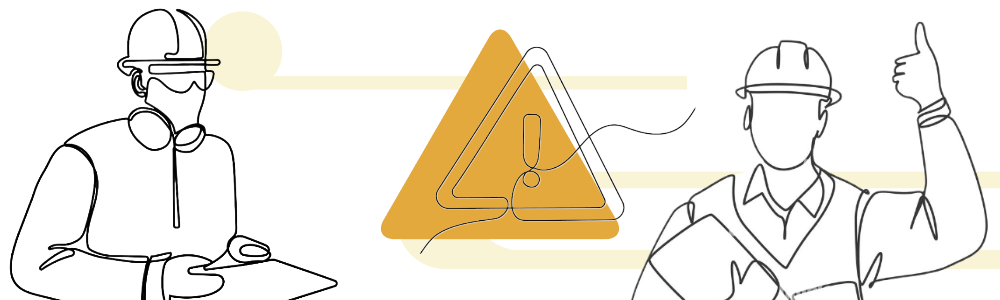
I. The danger of routine
In industrial environments, repetitive tasks often lead to routine. Workers who perform the same actions every day may lose vigilance. This phenomenon is explained psychologically by the concept of “habituation,” in which the response to a constant stimulus decreases. Habituation in the workplace can have serious consequences, such as ignoring safety procedures or failing to notice new risks. For example, construction workers frequently exposed to moving vehicles become less responsive to warning alarms, increasing their risk of accidents. Despite safety training, workers may still prioritize tasks over safety, illustrating the challenge of altering deep-seated habits.
Best practice
To address the risk of habituation in industrial environments, it is effective to introduce varied and unexpected safety training. This keeps workers alert and engaged. Technology such as portable monitoring devices can also help by providing alerts at signs of inattention or fatigue. In addition, a culture of mutual responsibility, where employees actively monitor each other for safe behavior, promotes overall safety. These approaches help break routine and increase workplace safety.
II. The danger of ergonomic overload
In industrial settings, ergonomic risks are often less noticeable but can lead to significant health issues over time. Workers performing repetitive tasks or using improperly set up workstations may develop musculoskeletal disorders, which can result in long-term disability and chronic pain. The subtle nature of ergonomic risks means they might not be recognized until they cause serious harm. Consider the case of assembly line workers in an automobile manufacturing plant. These employees typically spend long hours performing repetitive tasks, such as installing parts or tightening screws, often while standing in a fixed position or reaching overhead. Over time, the repetitive nature of these tasks, combined with the static posture and poor ergonomic setup of their workstations, can lead to significant ergonomic overload. Common issues that may arise include chronic lower back pain from prolonged standing, shoulder and neck strain from overhead work, and wrist injuries like carpal tunnel syndrome due to repetitive hand movements.
Best practice
To prevent ergonomic overload in industrial settings, it is crucial to implement ergonomic interventions that focus on both the physical workspace and worker behaviors. Begin by conducting thorough ergonomic assessments of all workstations to identify potential risk factors for musculoskeletal disorders. Adjust workstations to fit the physical dimensions of each worker and the specific tasks they perform. For example, ensure that work surfaces are at an appropriate height to avoid unnecessary bending or reaching, and provide adjustable seating to support proper posture. Additionally, integrate regular ergonomic training programs to educate workers on the importance of proper body mechanics. Encourage employees to practice stretching and take micro-breaks to relieve muscle tension throughout the day. Introducing job rotation can also be beneficial, allowing workers to switch between tasks and reduce the strain caused by repetitive motions.
III. The danger of understating risks
In industrial environments, the consequences of underestimating risks can be disastrous. Often, hazards known within the industry, such as chemical hazards, are not treated with due seriousness due to cost considerations, regulatory complexity, or a culture that does not prioritize safety practices. For example, although many companies are aware of the risks of chemical exposure, the lack of concrete action or minimal compliance with safety regulations can lead to serious health problems. This is often caused by a culture that values short-term productivity over long-term employee health. The risk is “hidden” by a lack of visible immediate effects, which reduces the sense of urgency.
Best practice
To effectively address the underestimation of risk in industrial environments, companies must establish a comprehensive safety management system that begins with in-depth risk assessments and ongoing monitoring to identify new and changing hazards. Leadership must demonstrate a strong commitment to safety by fostering a culture where safety training is conducted regularly and extensively and open communication about hazards is encouraged. Compliance with legal standards and involving employees in discussions and decisions about safety is also critical.
IV. The danger of shift work disorder
Shift work, especially night shifts and rotating shifts, can disrupt workers’ daily rhythms, leading to shift work disorder. This disorder includes a variety of symptoms such as insomnia, excessive sleepiness and can also lead to more serious psychological problems such as depression and anxiety. A study by the European Foundation for the Improvement of Living and Working Conditions found that about 20% of European shift workers suffer from symptoms related to shift work disorder. In a Swedish car factory, shift workers showed higher absenteeism and lower overall job satisfaction. After consulting with experts, the company implemented a more flexible shift scheduling system, giving workers more control over their working hours and reducing the need to rotate at night. These changes led to an improvement in mental health reports among employees and a decrease in absenteeism.
Best practice
To manage the psychological risks of shift work in the industrial sector, it is essential to implement flexible schedules that minimize disruption to workers’ natural rhythms. Companies should implement systems that give workers more say in their shift patterns, potentially reducing the need to work nights. In addition, offering health screenings aimed at identifying symptoms of shift work disorders and facilitating access to mental health services can help reduce negative effects on employee well-being. Education programs that inform workers about the importance of sleep hygiene and strategies for coping with irregular working hours are also vital.
V. The danger of inconsistent contractor safety standards
Managing contractors in industrial settings presents significant risks due to varying safety training levels and compliance standards across different firms. This disparity becomes particularly hazardous when contractors with different safety cultures and protocols work on the same project, increasing the potential for misunderstandings and accidents. For instance, in a multinational facility upgrade project in Belgium, a lack of standardized safety practices led to a critical oversight when a subcontractor unfamiliar with the host company’s strict lockout/tagout procedures initiated machinery that was under maintenance, resulting in severe injuries. This incident underscores the crucial need for harmonized safety standards to ensure all contractors are uniformly informed and compliant with the host company’s safety expectations.
Best practice
To effectively manage safety standards among diverse contractor groups, it is vital to establish a centralized safety induction system that aligns all contractors with the host company’s safety protocols upon their arrival at the site. This system should include mandatory, tailored safety training that addresses specific risks associated with the project, reinforced by regular audits to ensure ongoing compliance. Additionally, incorporating stringent safety clauses in contract agreements and fostering a collaborative safety culture through regular cross-company safety workshops can help bridge different safety practices, ensuring a cohesive and safe working environment for all personnel involved.
Get control of contractor safety with Onyx One
Ensure full safety compliance by all contractors with Onyx One. We understand all contactor risks and can help you implement a unified approach to protect your projects and the people on your site. Contact Onyx now and take the lead in proactive safety management!