Managing safety risks with subcontractors
Safety is a critical shared responsibility between main contractors and subcontractors. In the EU, laws like Directive 89/391/EEC require employers, including contractors, to ensure safe working conditions for all, including subcontractors’ employees. National laws further emphasize this duty.
To manage these risks, main contractors must prequalify subcontractors, regularly inspect safety practices, and maintain up-to-date documentation. Failing to do so can result in liability, fines, and reputational damage.
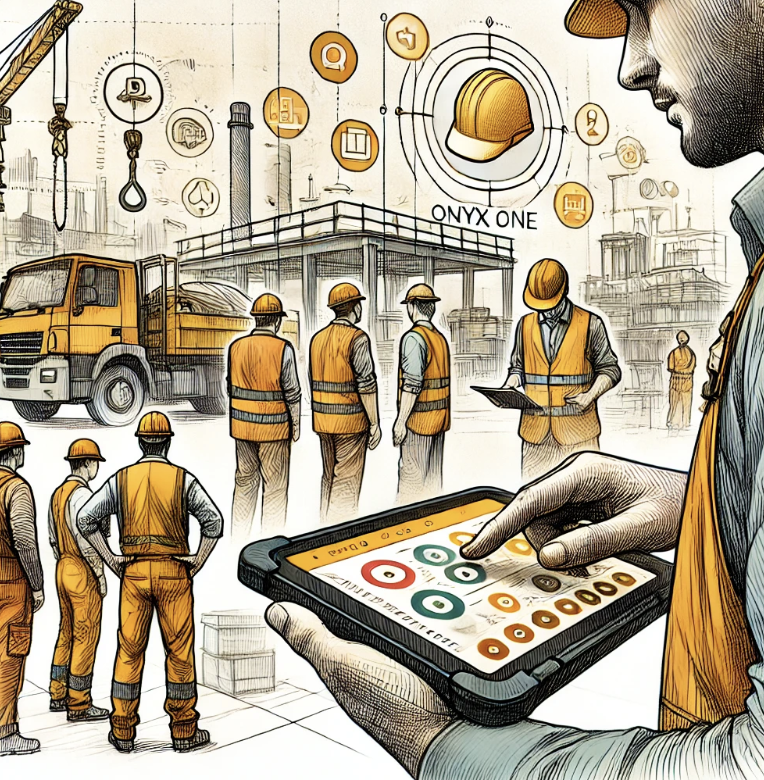
Shared responsibility for safety
Click on the links to download the corresponding documents.
In the European Union, the EU Directive 89/391/EEC on health and safety at work states that employers, including main contractors, must ensure that working conditions are safe for all employees, including those working for subcontractors. National laws, such as the Arbeidsomstandighedenwet (Arbowet) in the Netherlands, Arbeitsstättenverordnung in Germany, and the Codex over het Welzijn op het Werk in Belgium, further outline these obligations.
Subcontracting regulations across the EU and its member states aim to ensure fair labor practices and prevent exploitation in complex supply chains. The EU has no direct legislation on subcontracting, but several countries have implemented measures to address liability and worker protection. Common themes across these regulations include limiting the length of subcontracting chains, increasing transparency and accountability, ensuring proper working conditions, and establishing joint liability mechanisms to protect workers’ rights and prevent social dumping. Companies engaging in subcontracting must carefully navigate these national and sector-specific rules to ensure compliance and ethical business practices.
This means that main contractors are responsible for the safety of subcontractors and their employees. If a subcontractor fails to meet safety standards, the main contractor can be held liable, facing fines from national authorities like the Inspectie SZW (Netherlands), Arbeitsinspektion (Germany), or the Federal Public Service Employment, Labour and Social Dialogue (Belgium).
Key risks in subcontracting
Risks for the Client/Project Owner
Quality control
Less direct oversight of subcontractors can lead to quality issues, potentially resulting in project delays, increased costs, and safety hazards.
Project delays
Poor coordination or performance by subcontractors can impact the overall project timeline and budget.
Liability for accidents
While contractors carry insurance, the client may still face partial liability for accidents on their property.
Financial risks
Unpaid subcontractors may file liens against the client’s property or make direct claims.
Compliance issues
The client may be held responsible for violations of labor laws, environmental regulations, or building codes by contractors or subcontractors.
Communication challenges
Multiple layers of contractors can hinder effective information flow to the client.
Reputational damage
Significant project issues due to subcontractor problems can harm the client’s reputation.
Intellectual property risks Subcontractors may gain access to sensitive information or designs, potentially leading to IP theft or unintended disclosure.
Cost overruns
Poor subcontractor management can lead to unexpected costs for the client.
Reduced control
The use of subcontractors can diminish the client’s direct control over project aspects.
Risks for the Main Contractor
Legal liability
The contractor may be held responsible for injuries to subcontractor employees, even if the subcontractor was at fault.
Regulatory fines
Violations of safety regulations by subcontractors can result in fines for the main contractor.
Financial risks
The contractor may be liable for unpaid wages or benefits of subcontractor employees in some jurisdictions.
Quality control challenges
Ensuring consistent quality across multiple subcontractors can be difficult and time-consuming.
Schedule management
Coordinating multiple subcontractors to meet project timelines can be complex and challenging.
Contractual disputes
Disagreements with subcontractors over scope, payment, or performance can lead to costly legal battles.
Safety management
Ensuring all subcontractors adhere to safety standards requires constant vigilance and can be resource-intensive.
Insurance and bonding issues Inadequate insurance coverage by subcontractors can expose the main contractor to additional risks.
Skill and resource gaps Subcontractors may lack necessary skills or resources, requiring the main contractor to fill these gaps at additional cost.
Overview of recent workplace incidents in European industries
- On February 21, 2024, in the Netherlands, two individuals lost their lives and several others were severely injured in a crane accident at a construction site.
- On February 16, 2024, in Italy, five people died due to a collapse at a construction location in Florence.
- On January 18, 2024, in France, two fatalities occurred when a wall collapsed during construction work.
- On December 11, 2023, in Sweden, five individuals died in an accident involving a construction lift in Sundbyberg.
- On October 30, 2023, in Germany, four people were killed when scaffolding collapsed in an elevator shaft on a construction site.
- On July 27, 2023, an explosion in a chemical plant in Tarragona, Spain resulted in one death and eight injuries.
- On May 25, 2023, two individuals died and one was seriously injured due to an explosion at a fireworks factory near Naples, Italy.
- On April 28, 2023, one person died and four were injured following an explosion at a chemical facility in Leverkusen, Germany.
- On March 22, 2023, two fatalities occurred due to an explosion at a chip factory in Donegal, Ireland.
- On February 7, 2023, one person died and two were injured in an accident involving a forklift at a distribution center in Tilburg, Netherlands.
- On January 21, 2023, three people lost their lives during an explosion at a biodiesel plant in La Canonja, Tarragona.
- On December 16, 2022, two individuals died and four were injured following an explosion at a pharmaceutical company in Jonzac, France.
Practical tips for main contractors to manage safety risks
Prequalify subcontractors
- Thoroughly evaluate subcontractors’ safety standards and performance history
- Review their safety programs, incident rates, and compliance with national regulations
- Assess their experience with similar projects and specific safety challenges
- Check references from previous clients or contractors
- Verify proper licensing, certifications, and insurance coverage
Regular safety inspections
- Conduct both scheduled and unannounced safety audits
- Use standardized checklists to ensure consistency in inspections
- Involve subcontractor management in some inspections to promote accountability
- Document findings and follow up on corrective actions
- Analyze trends in inspection results to identify recurring issues
Joint Safety Meetings
- Hold regular safety meetings involving all subcontractors
- Encourage open discussion of safety concerns and near-miss incidents
- Share lessons learned from other projects or industry best practices
- Recognize and reward good safety performance
- Use these meetings to reinforce project-specific safety requirements
Technology integration
- Use Contractor Management Software to track compliance and incidents
- Implement wearable technology or IoT devices to monitor high-risk areas or activities
- Use digital platforms for real-time reporting and communication of safety issues
Clear contract terms
- Include detailed safety responsibilities and expectations in contracts
- Specify adherence to project-specific safety plans and procedures
- Outline consequences for safety violations or non-compliance
- Include provisions for safety training requirements
- Clearly define reporting procedures for incidents and near-misses
Proper documentation and monitoring
- Maintain up-to-date safety documentation, including risk assessments and safety plans
- Implement a system for tracking safety metrics across all subcontractors
- Regularly review and update safety procedures based on project progress and changing conditions
- Ensure proper record-keeping of all safety-related activities, training, and incidents
Comprehensive Safety Training
- Provide site-specific safety orientation for all subcontractor employees
- Offer additional training for high-risk activities or new equipment
- Ensure subcontractors’ employees understand emergency procedures
- Verify that all required certifications are current and relevant
Clear communication channels
- Establish clear lines of communication for safety issues
- Designate specific points of contact for safety matters within each subcontractor’s team
- Implement a system for quick dissemination of safety alerts or changes in procedures
- Encourage reporting of safety concerns without fear of retaliation
Streamline safety and compliance with Onyx One
Main contractors face significant risks in terms of liability, fines, and reputation damage if they fail to properly oversee subcontractors’ safety practices. By taking proactive steps such as prequalifying subcontractors, conducting regular safety inspections, and maintaining up-to-date documentation, main contractors can effectively manage these risks and create a safer work environment for everyone involved.
This is where Onyx One comes in. The Onyx One Contractor Management System provides a comprehensive solution that simplifies these processes. By offering a centralized platform for contractor qualification, personal certification, and job assignments, Onyx One ensures that contractors and subcontractors meet all necessary safety standards, reducing administrative burdens and improving compliance. The system also enhances communication and transparency, helping contractors streamline their workflows and avoid potential risks while maintaining the highest safety standards​​​.
WHY
WE BELIEVE IN TEAMWORK
I believe that the world is a better place when: Everyone gets to do what they love.
- Everyone does what they do best.
- We can focus on what we do best.
- We have the opportunity to specialize, which means we need others to do what we’d prefer not to, i.e., partnerships and teamwork are a must.
In short, I believe that the world is better off when we work together. Teamwork for the efficient and sustainable use of resources. Teamwork with our colleagues, suppliers, customers, and distribution channels. Teamwork with specialists, consultants, and contractors…and with the government in a regulatory framework. - Teamwork as individuals within a team.
- Teamwork as a team within an organization.
- Teamwork as a business in society.
- I believe that partnerships and teamwork are possible through personal development. Teamwork happens when we:
- are prepared for our mission
- know what’s expected of us
- have the autonomy to make (the right) decisions
- are confident that what we delegate will be done well
- trust that others are also prepared, have invested in personal development, and know what’s expected of them
WHAT
WE BELIEVE IN QUALITY AND HONESTY
We believe that work and teamwork only happen with these values as our lodestar:
We believe that work and teamwork only happen with these values as our lodestar:
- Equality
- Low-ego
- Independence
- Respect
- Appreciation
We believe that products and services will excel because of our:
- Focus
- Care
- Professionalism
We support and stand for:
- Individuality
- Originality
- Flexibility
- Fun
We believe in making a positive contribution to society and the whole world.
We believe that our focus on data security in accordance with ISO 27001 and the GDPR delivers added value to our customers through, e.g.:
- Privacy by design (for developments or designs)
- Privacy by default (using default settings)
- Partnering with the supervisory authority where needed
- Doing our jobs as processors and controllers well
HOW
WE BELIEVE IN TECHNOLOGY AND EFFICIENCY
We help companies:
- Train their employees
- Make training processes more efficient
- Gain insight into their employees’ development
And that’s why we develop e-learning courses and provide the Onyx learning environment.
We help clients:
- Train and qualify their contractors
- Gain insight into their contractors’ competencies
- Be prepared when contractors arrive for work Manage their teams
We help contractors:
- Efficiently get ready for work
- Simplify their administration
We help manufacturers:
- Train their distribution channel
- Inform their customers
That’s why we’ve developed Onyx One and are creating an online community of the most efficient companies.