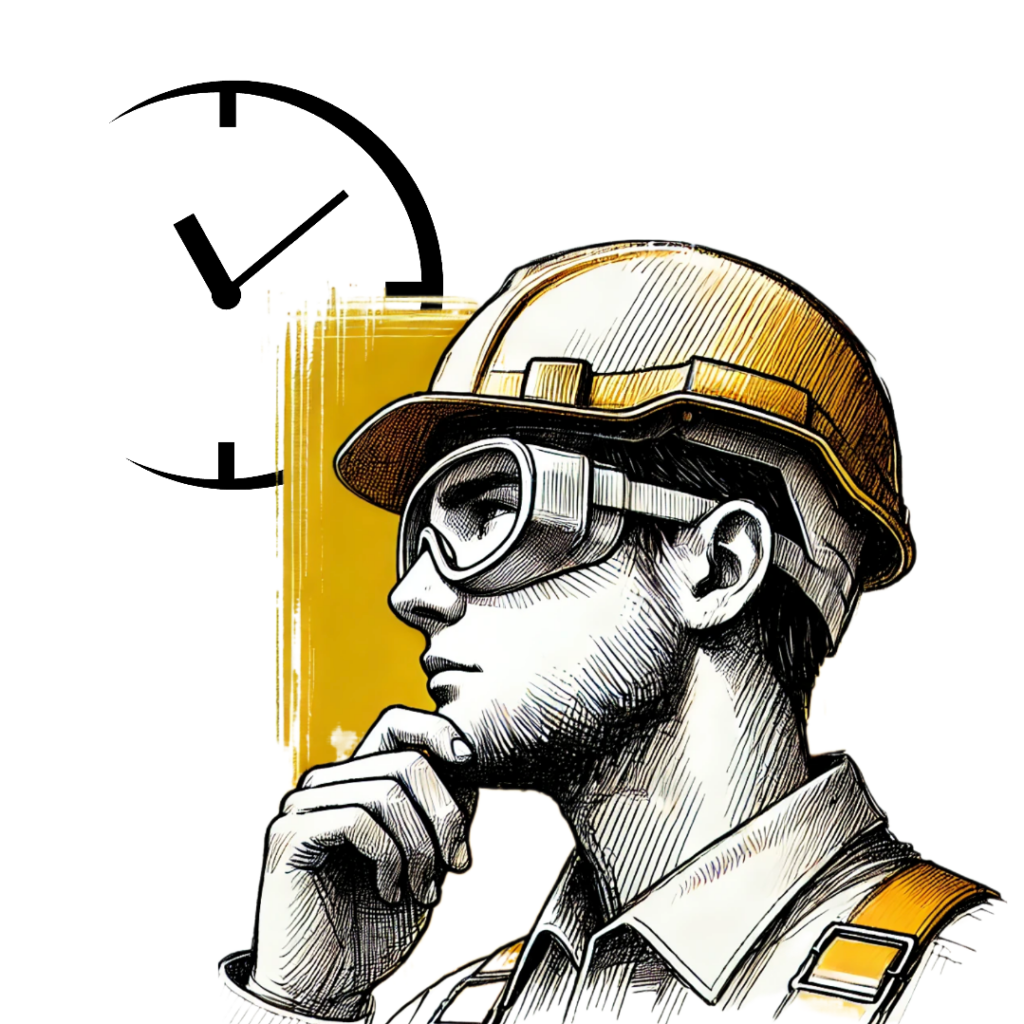
Industrial companies increasingly need flexibility. They rely on temporary workers and contractors for project work, seasonal peaks, and to quickly respond to market changes. This reduces fixed costs and increases adaptability. But how do you ensure that safety standards remain high while the workforce is constantly changing?
The Challenge Flexibility without compromising safety
Temporary workers often come from diverse backgrounds and have varying levels of experience. While permanent employees are familiar with safety protocols, this is not always the case for temporary staff. Research shows that temporary workers are 50% more likely to be involved in workplace accidents. This is largely due to a lack of experience or insufficient knowledge of the specific safety rules on-site.
Additionally, temporary workers tend to feel less connected to the company. Since they work for a short period, they often feel less responsible for adhering to safety regulations. This makes it more difficult to maintain a strong safety culture.
How to Combine Flexibility and Safety
Quick and targeted onboarding
Temporary workers have little time to get up to speed. Long onboarding programs are not feasible. Successful companies use e-learning modules or VR training to quickly familiarize contractors with key safety rules. In just a few hours, they learn the critical information they need.
A logistics company reduced the onboarding time for contractors by 40% by implementing a digital learning platform. Each contractor only took the training relevant to their specific task.
Use technology for monitoring
Technology plays a vital role in safety management. With wearable devices or IoT sensors, you can monitor contractors in real-time and immediately detect any deviations. For example, sensors can detect whether personal protective equipment is being worn or issue an alert when someone leaves a safe zone.
A construction company that introduced wearable safety equipment saw a 25% reduction in safety incidents among temporary workers. Contractors gained real-time insights into their behavior on the job site.
Flexible safety programs
A one-size-fits-all safety program doesn’t work for a diverse workforce. Successful companies tailor their programs to each contractor’s experience and tasks. Experienced workers can quickly take on complex tasks, while less experienced employees receive additional training.
Permanent safety coordinators
Flexibility requires a permanent point of contact for safety. Dedicated safety coordinators ensure that standards remain high, regardless of who is on the work floor. They perform daily checks to ensure safety guidelines are being followed and provide contractors with the necessary support.
At a chemical plant, a permanent safety coordinator conducts a daily briefing. This ensures that all contractors, regardless of experience, are aware of the risks on-site.
Ensure both flexibility and safety. Onyx One makes it easy to manage contractors flexibly, track their certifications, and ensure that safety standards are always upheld, even with changing teams.